ENGEL slaví úspěch s Lightweight Future Day
Lehkost je na vzestupu jako klíčová technologie na cestě k CO2 neutrálnímu světu při dosahování cílů ochrany klimatu. Hlavní roli v tomto trendu budou hrát termoplasty, což potvrdila akce Lightweight Future Day 2021 pořádaná společností ENGEL.
„I když virtuální platforma letos dosáhla obzvláště vysoké úrovně pokrytí, osobní kontakty jsou pro nás stále důležité. Těšíme se, až příští rok opět nabídneme Lightweight Future Day jako face-to-face nebo hybridní akci a uvítáme co nejvíce účastníků v našem závodě ve Schwertbergu,“ říká Christian Wolfsberger, manažer pro rozvoj podnikání Lightweight Composites ve společnosti ENGEL a organizátor akce.
Pro účastníky je akce Lightweight Future Day cenná nejen kvůli možnosti výměny zkušeností a znalostí mezi výrobci strojů a dodavateli systémů, materiálů, výrobci forem, výzkumníky a vývojáři, ale i proto, že dochází k interakci a spolupráci mezi průmyslovými odvětvími, která jsou jinak zcela odlišná, ale hledají řešení podobných výzev.
Na letošním ročníku představili nejmodernější řešení a přístupy špičkoví odborníci ze všech důležitých uživatelských odvětví, jako je automobilový průmysl, konstrukce jízdních kol a motocyklů, letectví, sport a volný čas, i zástupci renomovaných výzkumných ústavů. Více než 500 účastníků získalo cenné postřehy z 15 klíčových přednášek představujících všechny aspekty současného vývoje a trendů v oblasti lehkých konstrukcí.
Termoplastové kompozity urychlují sériovou výrobu
Jak uvedl v úvodní přednášce Michael Thienel, odborník na vývoj dveřních řešení u automobilového dodavatele Brose, díky termoplastickým kompozitům a odpovídající výrobní technologii je velkosériová výroba mnohem jednodušší. Díky inteligentní kombinaci materiálů firma vyvinula inovativní dveřní systém, který ve srovnání se staršími výrobky na bázi oceli umožňuje ušetřit až 5 kg, tj. 40 % hmotnosti, při zachování stejné bezpečnosti při nárazu. Navíc se podařilo dosáhnout tloušťky stěny pouhých 0,6 mm. Společnost dodává od roku 2018 automobilce Ford milion dveřních modulů vyrobených z termoplastů vyztužených vlákny (termoplastická fólie) ročně a dnes je Brose již na prahu sériové výroby další generace dveřních modulů.
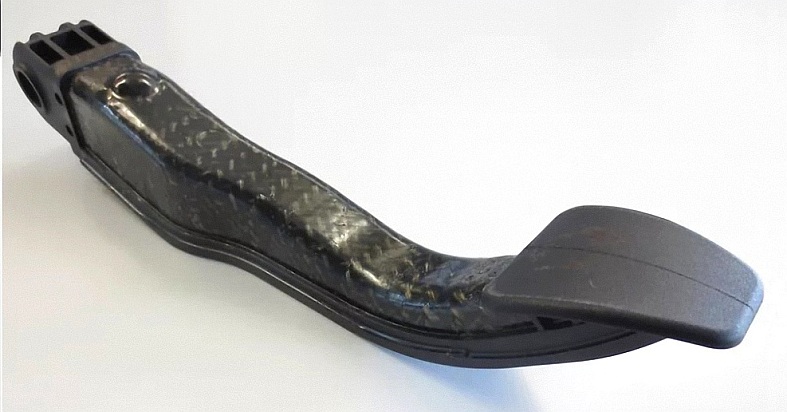
Nový konstrukční prvek nahrazuje jinou, původně ocelovou část. Celkově to ušetří další kilogram hmotnosti na automobilu a systém je i cenově výhodnější než ocelová varianta.
Mnoho klíčových přednášek na Lightweight Future Day ukazuje, že cestou k nejmodernější lehké technice je často termoplastické zpracování. Termoplasty podporuje i společnost FACC, specialista na lehké komponenty v leteckých konstrukcích, která se zaměřuje na budoucí trh „Urban Air Mobility“ leteckých kabin s posádkou a bezpilotních dronů v městském provozu. Jak uvedl ředitel výzkumu a technologie společnosti Rene Adam, očekává se objem výroby od 5000 do 30 000 komponent za rok, což jsou výrazně vyšší čísla ve srovnání s výrobou dílů pro větší letadla, dosahující zhruba 1000 ks ročně. Vzhledem ke svým dlouhým dobám vytvrzování by termosety, dosud primárně používané v konstrukci letadel, nemohly splnit zde požadované krátké doby cyklů. Termoplasty však budou pravděpodobně v budoucnu hrát větší roli také při stavbě tradičních letadel, protože letecký průmysl si stanovil za cíl dosáhnout klimatické neutrality do roku 2050.
„Výrobní procesy v leteckém průmyslu se zcela změní. Lepení za studena a rychlé tváření se zde ještě nestaly standardními procesy, je nutné výrazně zlepšit nákladové struktury a výrobní cykly, ale FACC je přesvědčena, že termoplasty budou klíčovým materiálem pro vláknové kompozitní plasty v letectví.
Případ použití švýcarské společnosti Svismold ukázal, že lehké materiály nabízejí výhody i v případech, kdy hmotnost není hlavní problém. Poté, co výrobce surfových prken nahradil předchozí termosetová žebra za řešení vyrobené z kompozitů z termoplastických vláken na bázi UD pásek se ukázalo, že nová ploutev nabízí bezkonkurenční vlastnosti přesnosti řízení, což vzbudilo nadšenou odezvu v surfařské komunitě. Jedním z důvodů je přesně vypočítaný tok síly v dílu, který lze přesně reprodukovat, protože použití UD pásky zajišťuje vyrovnání vláken a současně snižuje výrobní náklady.
Recyklace činí lehké konstrukce udržitelnější
Dalším tématem byla v mnoha prezentacích vynikající recyklovatelnost termoplastů ve srovnání s omezenější recyklovatelností termosetových vláknových kompozitních materiálů. Firma Forward Engineering v rámci studie porovnala stopu CO2 při výrobě brzdového pedálu na základě primárních termoplastů, biologických materiálů a recyklovaných termoplastů a potenciál úspor CO2 při používání termoplastů s recyklovaným obsahem se ukázal jako významný.
„Věříme, že termoplastické materiály mají velký potenciál z hlediska udržitelnosti. Aby toho bylo možné využít, je nyní třeba zavést recyklační procesy v průmyslovém měřítku," uvedl Georg Käsmeier ze společnosti Forward Engineering.
Vzhledem k rostoucímu významu termoplastů v lehkých hmotách firma ENGEL v posledních letech značně investovala do technologií a systémů pro zpracování termoplastických kompozitů.
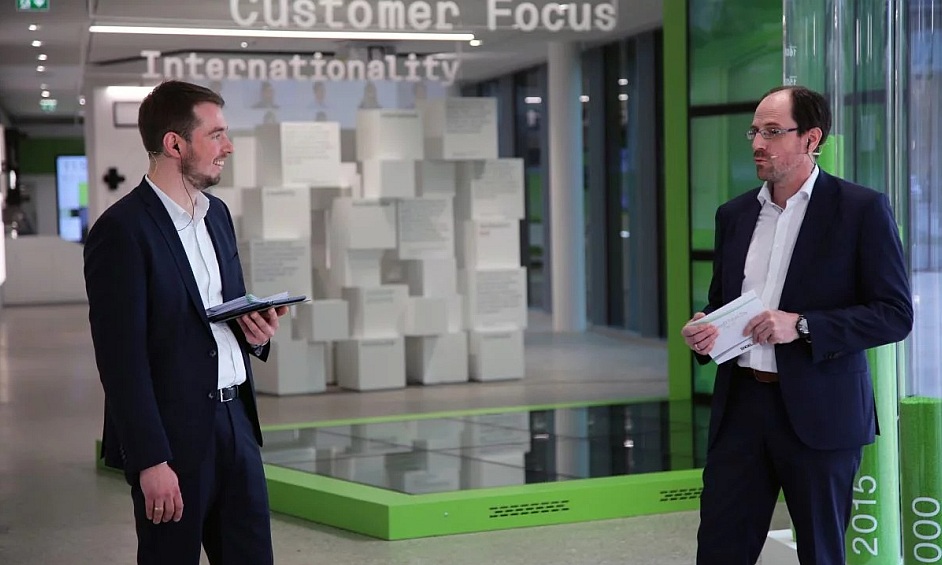
„Jsme první společností na světě schopnou nabídnout plně integrovaný proces, který začíná buňkou pro pokládku UD pásky a končí plně konsolidovanou, tvarovanou termoplastickou lehkou součástí,“ řekl Paul Zwicklhuber, vývojový inženýr divize Composite Processing společnosti ENGEL. Buňka pro pokládání pásky využívající princip pick-and-place umožňuje bodově svařit pásky a ukládat je v intervalech tří až čtyř sekund. Protože kvalita závisí do značné míry na přesnosti umístění pásky, vybavil ENGEL pokládací celu měřicím systémem s kamerovou technologií, za nímž následuje konsolidační jednotka, která upravuje termoplastické páskové tkaniny během vstřikovacího cyklu. Konsolidaci lze bezproblémově integrovat do celkového procesu, což významně zvyšuje efektivitu výroby páskových řešení na míru.
Jádrem integrovaného řešení je proces ENGEL Organomelt (používaný mj. při výrobě dveřních modulů Brose). Zde se tvoří a funkcionalizují kompozitní prepregy z termoplastických vláken, jako jsou UD pásky a organické fólie. Funkční prvky, jako jsou výztužná žebra nebo montážní prvky, lze ihned po tvarování za tepla vytvarovat pomocí termoplastu ze skupiny matricových materiálů. To umožňuje vysoce integrovaný a plně automatizovaný výrobní proces a současně tento proces zjednodušuje recyklaci dílů na konci jejich životnosti.